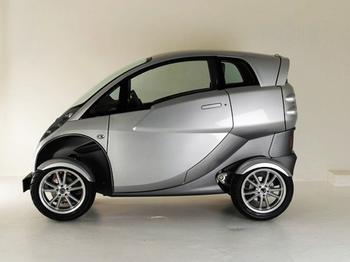
Recently, the author went to Leipzig to participate in the i2013 Innovation Day organised by the BMW Group for global journalists. Through the observation of the entire process from renewable energy to body manufacturing, to maintenance and recharging, the electric vehicle can be found in the automotive industry and The revolution brought by the automobile society is not merely a substitute for the power mode and the meaning of energy saving and emission reduction for mobile terminals.
For traditional automobile manufacturing, its negative externalities have been underestimated, especially in China's booming emerging markets. Behind the positive effects such as boosting local GDP growth, stimulating regional economy, and promoting employment, the negative externalities such as the contribution of PM2.5 and dependence on crude oil imports have become increasingly unnoticed. In this context, responsible manufacturers will increasingly focus on energy-saving and emission reduction throughout the value chain.
The BMW i3, which will be launched in September this year, also seeks to minimize the adverse impact of production on the environment. Therefore, in its manufacturing process, it pays more attention to environmental protection in terms of energy supply, water consumption, solvent emissions, and waste disposal. For example, in the production and processing of carbon fiber reinforced plastic (CFK), the electricity used in the Moses Lake plant in the United States is generated by hydroelectricity, and the electricity demand in the Leipzig plant in Germany will rely entirely on local wind power. The author understands that the direct establishment of wind power generation equipment for the production of electricity supply at the automobile manufacturer's factory site is the first of its kind in Germany. In addition to the CO2 zero-emissions power supply, the Leipzig plant can save an additional 50% of energy and 70% of the water used in the production of i models compared to BMW’s existing production average.
A lot of reporters at automobile production plants have visited and the noise of the press shop often needs earplug protection to deal with it. However, in the press shop of the Leipzig factory, which is preparing to mass-produce the i3, carbon fiber-reinforced plastic is used instead of the heavy steel plate. Body building and deafening noises can be said for goodbye. This is another kind of work for the workshop workers. Green. The new precision tools also led to a revolution in body manufacturing, with no noise from screws or rivets, no sparks during welding, advanced adhesives, and full automation. The body that was glued up sounded incredible, but it was true that it was as strong as the welded steel plates.
Will the use of lightweight carbon fiber bodies cause inconvenience in maintenance and repair? During the visit, the reporter also found the answer: Due to accidents caused by body damage, due to the importance of ease of maintenance in the automotive design stage, so BMW developed a time-saving repair method specifically for the plastic shell and i3CFK parts. As a result, the overall cost of accident repairs was equal to that of the BMW 1 Series. At present, BMW Group is negotiating with the German insurance industry for the cost of i-electric vehicles.
The sustainable theme has been very important to the BMW electric car project from the beginning and it has been carried through to the entire value creation chain. Therefore, the i model's manufacturing process also pays great attention to the recycling of materials, and has developed a unique recycling process for the recycling of waste, this process has been able to adapt to the needs of mass production. Different processes are used to re-use high-quality materials from scrapped vehicles in production, even accident vehicle/vehicle manufacturing. At present, about 10% of the carbon fibers used for producing i3 are recycled materials. The use of "secondary CFK fibers" is part of the recycling process of sustainable materials. Resources have been saved and protected, and future applications of raw materials have also been guaranteed.
In the charging stage, if there is a modern public quick charge device, it can charge 80% of the battery in just 30 minutes, which means that you can charge the battery for another lunch or city shopping time and then drive for 120 kilometers. The power needed. Looking into the future, inductive charging is promising. No cables and connectors are required. Vehicles rely on electric drives above the bottom pallets, and energy is transmitted through the electromagnetic field without contact. This can theoretically be used for home garages, but it is only possible to promote them to the public domain when such devices are installed in streets and public parking lots.
In the field of public charging, there are currently more than 70 different providers of public charging facilities in Germany. These suppliers still use different payment and service methods. Regional coordination is very necessary. "Immediate charge card" is a product independently developed by the i project. It has now shown the ability to provide intelligent solutions for customers. What will soon become a reality is that from Munich to Leipzig, which relies solely on electric power - a temporary organization of BMW, Siemens, etc. will build several fast charging stations along the A9 highway within the framework of a funded project. In early 2014, a purely electric drive from Munich to Berlin with only a few stops at a charging station is possible.
These examples show that the shared charging infrastructure is steadily growing and complements the possibility of charging mainly at home or in the workplace. As a result, users of electric vehicles will get more flexibility and possibilities, and can easily travel longer distances. In this case, BMW's large-scale field experiments have yielded interesting results: Mini-E users can use their own or secure public charging method to power 90% of the routes, and the average public charging part is less than 10%.
The reporter has always been concerned about the development of the international electric vehicle industry. Rational analysis, compared with the early stage of the international financial crisis, some speculative elements in the industry are slowly ebbing, but the pace of global industrialization of electric vehicles has not been stagnant, and the rescue role of electric vehicles in the context of global warming and petrochemical energy pressure is the slightest Not weakened. The strange thing is that there is always a feeling of impetuousness in the domestic auto industry, and it is always an artificial opposition between the general hybrid and pure electric technology. Even the Shanghai International Auto Show as the evidence of the "rising" of electric vehicle-type micro-hybrids, or the hybrid decentralized electric vehicles on the change of new energy subsidy, is actually a completely counterfeit opposition. For major auto groups, hybrid power has been used as an ordinary energy-saving technology. However, hybrid power does not have the revolutionary significance of reshaping the auto industry and society as pure electric power.
For the Chinese auto industry, it is necessary to make use of technologies such as unplugged hybrid power in the near future to make greater use of the energy-saving and emission-reduction functions of on-sale vehicles, and to pay attention to the research and development of pure electric drive technology from a strategic perspective. At the national macro level, attention should be paid to the support of key industrial clusters including motors, batteries, electronic control, and light weight of the auto parts. For self-branded products driven by pure electric power, appropriate support should be given for project approval and government procurement. The pure electric drive products of the joint venture should encourage the use of "joint ventures' own brands" and reasonably seek the balance of the best interests of the Chinese and foreign parties.
Eco Solvent Inkjet Coating For Canvas
Eco Solvent Inkjet Coating For Canvas,Canvas Fabric ,Canvas Material ,Cotton Canvas Fabric
Guangzhou Quanxu Technology Co Ltd , https://www.silicamattingagent.com