Model NO.: TG219
Line Speed: Please Check Below
Thickness: Please Check Below
Trademark: TGMCO
Transport Package: Wood Box
Origin: China
HS Code: 8515219100
Model NO.: TG219
Line Speed: Please Check Below
Thickness: Please Check Below
Trademark: TGMCO
Transport Package: Wood Box
Origin: China
HS Code: 8515219100
Slited coil is uncoiled and feed into forming section passing through the equipment of entry section. Entry section enables tube mill to run continuously by using strip joining and accumulator. Before welding, pipe is formed in round shape passing through a series of driven and idler rollers of forming section. In welding section pipe is longitudinally welded by using high frequency induction welding method. Outside bead is removed and formed in shape of scrap. The weld seam is ironed and pipe passes through the cooling section. Then in sizing section, pipe is formed to specified size and converted into specified shape. After sizing, pipe is cut to required length by using flying saw cut off equipment and delivered to collecting table after passing through run out conveyor.Main Specifications
Below is our standard tube mills table, we can customize machines as per customer special requirements
Model | Round Pipe | Square Pipe | Rectangular Pipe | Thickness |  Pipe Length | Line Speed |  Welding Type | High Frequency Power/KW |  Standard |
TG16 | 7.5 - 16 mm | / | / | 0. 4 - 1.0 mm | 4.0 - 10.0 meters | Max. 120 m/min | Solid State High Frequency Welding | 60 | / |
TG20 | 10 - 25.4 mm | Â 10 x 10 - 20 x 20 mm | Â 10 x 20 - 10 x 30 mm | 0.4 - 1.0 mm | 4.0 - 10.0 meters | Max. 120 m/min | Solid State High Frequency Welding | 60 | / |
TG32 | 12.7 - 38.1 mm | Â 10 x 10 - 30 x 30 mm | Â 10 x 20 - 40 x 20 mm | 0. 5 - 1.8 mm | 4.0 - 10.0 meters | Max. 120 m/min | Solid State High Frequency Welding | 100 | / |
TG45 | 15.0 - 50.8 mm | Â 12 x 12 - 40 x 40 mm | Â 10 x 20 - 50 x 30 mm | 0.6 - 2.0 mm | 4.0 - 10.0 meters | Max. 100 m/min | Solid State High Frequency Welding | 150 | / |
TG50 | 20.0 - 63.5 mm | Â 15 x 15 - 50 x 50 mm | Â 10 x 20 - 60 x 40 mm | 0.8 - 2.75 mm | 4.0 - 10.0 meters | Max. 100 m/min | Solid State High Frequency Welding | 200 | / |
TG60 | 25.4 - 76.4 mm | Â 20 x 20 - 60 x 60 mm | Â 10 x 30 - 80 x 40 mm | 1.0 - 3.0 mm | 4.0 - 10.0 meters | Max. 90 m/min | Solid State High Frequency Welding | 250 | / |
TG76 | Â 31.8 - 89.0 mm | Â 25 x 25 - 70 x 70 mm | Â 20 x 30 - 100 x 40 mm | 1.0 - 3.75 mm | 4.0 - 10.0 meters | Max. 80 m/min | Solid State High Frequency Welding | 300 | / |
TG89 | 38.1 - 102.0 mm | Â 30 x 30 - 80 x 80 mm | Â 20 x 40 - 100 x 60 mm | 1.0 - 4.0 mm | 4.0 - 10.0 meters | Max. 80 m/min | Solid State High Frequency Welding | 300 | / |
TG114 | 38.1 - 114.3 mm | Â 30 x 30 - 90 x 90 mm | Â 20 x 40 - 60 x 120 mm | 1.0 - 4.0 mm | 4.0 - 10.0 meters | Max. 70 m/min | Solid State High Frequency Welding | 300 | / |
TG125 | 63.5 - 127 mm | Â 50 x 50 - 100 x 100 mm | Â 60 x 40 - 150 x 50 mm | 2.0 - 5.0 mm | 4.0 - 10.0 meters | Max. 60 m/min | Solid State High Frequency Welding | 400 | / |
TG165 | 76. 2 - 165 mm | Â 60 x 60 - 130 x 130 mm | Â 80 x 40 - 140 x 120 mm | 2.0 - 6.0 mm | 4.0 - 10.0 meters | Max. 60 m/min | Solid State High Frequency Welding | 500 | / |
TG219 | 89.0 - 219.0 mm | Â 70 x 70 - 170 x 170 mm | Â 80 x 60 - 140 x 200 mm | 2.0 - 8.0 mm | 4.0 - 10.0 meters | Max. 60 m/min | Solid State High Frequency Welding | 600 | / |
API&ERW 168 | 76.2 - 168.0 mm | 60x60 - 130x130Â mm | 80x40 - 150x100Â mm | 2.0 - 8.5 mm | 5.0 - 12.0 meters | Max 60Â m/min | Solid State High Frequency Welding | 600kw | API 5LX, API 5L A&B, ASTM A53 A&B, up to API X-70 |
API&ERW 219 | 89.0 - 219.0 mm | 70x70 - 170x170Â mm | 80x60 - 200x140Â mm | Â 3.0 - 10.0 mm | 5.0 - 12.0 meters | Max 55Â m/min | Solid State High Frequency Welding | 800kw | |
API&ERW 325 | 114.0 - 325.0 mm | Â 90x90mm - 250x250Â mm | Â 80x100- 200x300Â mm | 4.0 - 12.5 mm | 5.0 - 12.0 meters | Max 40Â m/min | Solid State High Frequency Welding | 1000kw | |
API&ERW 508 | 165.0 - 508.0 mm | 130x130 - 400x400Â mm | 120x140 - 350x450Â mm | 6.0- 12.7 mm | 5.0 - 18.0 meters | Max. 30Â m/min | Solid State High Frequency Welding | 1000kw |
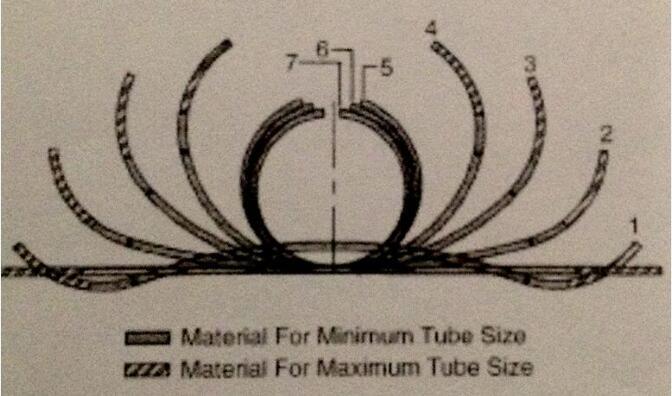
Flow Chart
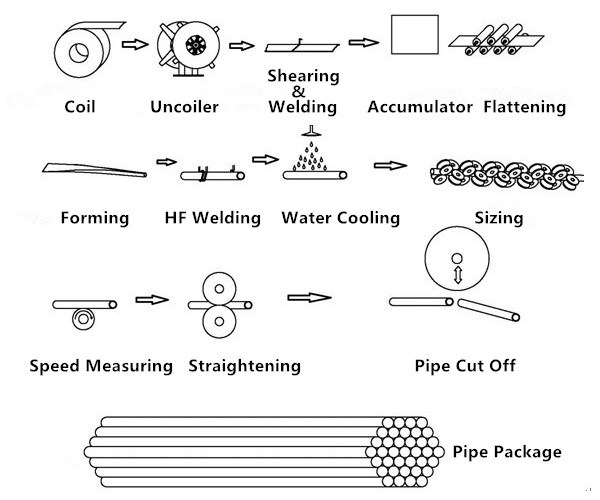
Step1: Uncoiler
Uncoiler the function is to support and expand the strip, so strip can enter into machine to roll forming. Strip can be expanded by hydraulic or pneumatic and uncoiler can be rotated 180 degree. Strip expand speed can be adjusted, braking device designed with pneumatic or hydraulic cylinder to press the brake rubber block
Step2: Shear & end welding
It is used to shear the head and the end of the steel strip of two steel coils, cutting off the irregular part then welding two steel strips, so machine can work continuously. Â
Step3: Accumulator
Installed between shear & end welder and forming mill, horizontal spiral accumulator store a large amount of strip in a reasonable footprint space to give enough time for shear & end welder to cut and join the ends of two successive coils with non-stop tube mill
It has vertical cage type accumulator for small size tube mill
Step4: Forming
The function of this part is to make the steel strip become to the tube blank by forming rollers
Step5: welding & scarfing
The function of this part is to center the welding seam and guide the tube blank to welding device, so the welding seam will be closed before welding, use scarfing tool to remove the burr to ensure the smooth welding
Step6: Sizing
The function of this part is used to finish the tube blank from the forming machine, so the tube size can meet the physical dimension as customer required, form to square and rectangular and other shape profiles
Step7: Straightening
4 rolls turk head straightening, straighten pipe online to achieve the ideal flatness
Step8: Cut off saw
Cut off the pipe with required length, length of pipe can be set
With option of cold saw and flying saw
Step9: Run out table
This unit is to convey the finished pipe to packing, pipe transmit by dynamic roll. A signal sensing device installed in the end of run out table, when pipe touch the signal sensing device, it will feedback the signal to control panel, control panel start working and discharge the pipe
Packing & Delivery
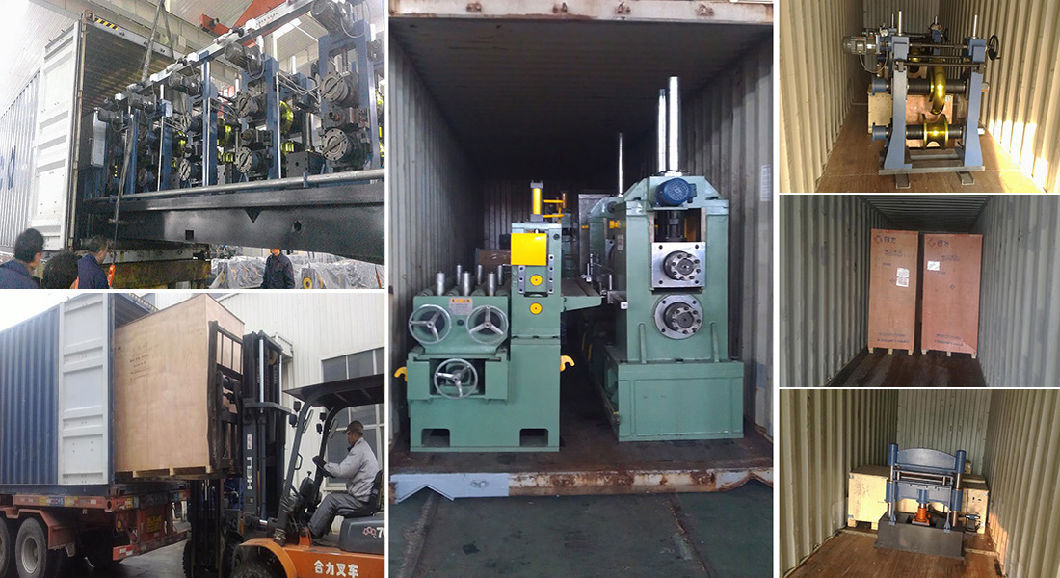
Not only the Good Machine, but also the Most Attentive Service
Integrity Solution & Turnkey Project
Creat the Value of Steel
 Slited coil is uncoiled and feed into forming section passing through the equipment of entry section. Entry section enables tube mill to run continuously by using strip joining and accumulator. Before welding, pipe is formed in round shape passing through a series of driven and idler rollers of forming section. In welding section pipe is longitudinally welded by using high frequency induction welding method. Outside bead is removed and formed in shape of scrap. The weld seam is ironed and pipe passes through the cooling section. Then in sizing section, pipe is formed to specified size and converted into specified shape. After sizing, pipe is cut to required length by using flying saw cut off equipment and delivered to collecting table after passing through run out conveyor.
Main Specifications
Below is our standard tube mills table, we can customize machines as per customer special requirements
Model | Round Pipe | Square Pipe | Rectangular Pipe | Thickness |  Pipe Length | Line Speed |  Welding Type | High Frequency Power/KW |  Standard |
TG16 | 7.5 - 16 mm | / | / | 0. 4 - 1.0 mm | 4.0 - 10.0 meters | Max. 120 m/min | Solid State High Frequency Welding | 60 | / |
TG20 | 10 - 25.4 mm | Â 10 x 10 - 20 x 20 mm | Â 10 x 20 - 10 x 30 mm | 0.4 - 1.0 mm | 4.0 - 10.0 meters | Max. 120 m/min | Solid State High Frequency Welding | 60 | / |
TG32 | 12.7 - 38.1 mm | Â 10 x 10 - 30 x 30 mm | oxy-hydrogen generator-carbon cleaning Carbon Cleaner,Carbon Remover,Car Wash Zhejiang Wanhao Machine Science And Technology Co., Ltd. , http://www.hkygenerator.com |