Product Description
 Plate for Heat Exchanger,Plate Heat ExchangerÂ
Company Profile
Shanghai Shengsheng Machinery Co., Ltd.. is specialized in manufacuturing plate heat exchanger,
plate and shell heat exchanger,plate heat exchanger plate,plate heat exchanger gasket and hydraulic press for forming plate.We can also provide plate heat exchanger mould,semi-welded plate heat exchanger,wide gap/free-flow plate heat exchanger.Â
Semi-welded plate heat exchanger is widely used in aggressive media for heating and cooling. One Semi-welded plate cassette is made of two corrugated heat exchanger plates which are mounted in a 180 angle to each other; back to back these are laser welded alongside the sealing groove provided for the gasket, the aggressive media flows through the inlet flow passages, and on the outside, each cassette is sealed with a gasket, when refrigerant passes from one cassette to the other, only two of the four ring gaskets at the apertures get in contact with the media.
PHE Plate Specifications | |
Model | Various type |
Material | 304SS,316SS,Titanium,ASMO254,Hastelloy C-276,Ni201,904L |
Thickness | >0.5mm |
Plate Hole | 0 Hole,1 Hole,2 Holes,3 Holes,4 Holes |
Package details | Standard export plywood case & customizing |
Production Capacity | 200000m²/year |
Â
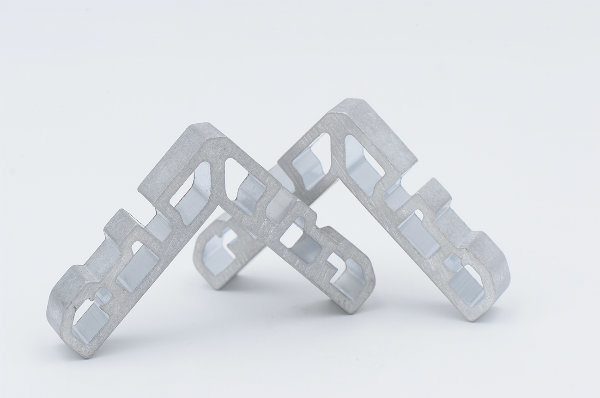
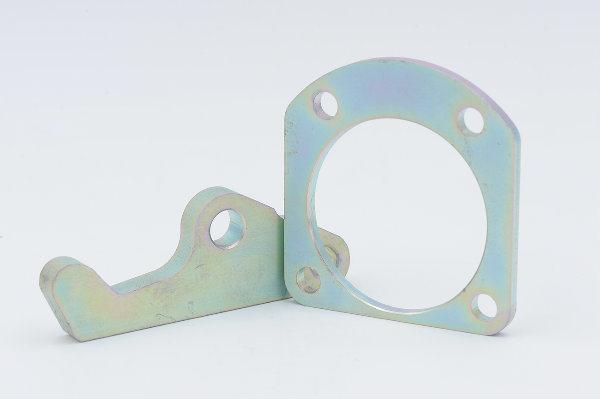
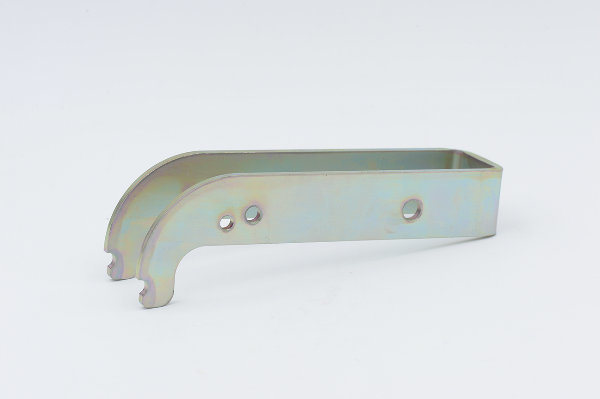
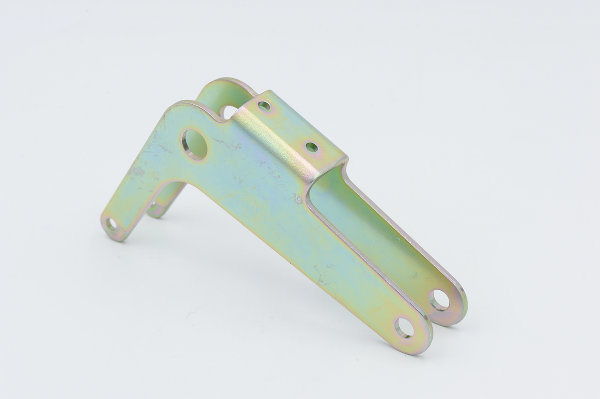
 Our Advantages
a. can provide various phe plates for all makes and models,and also make plate mould according to
customer requirements.
b. are supplier of phe replacement plates for GEA,Tranter,Sondex,Funke,Thermowave,APV.
c. not only produce conventional plates, but also special plates, such as semi-welded,free-flow,double-wall plates.
d. designing and calculating new PHE according to technical specification provided by customers in different
industry conditions.
e. high quality,reasonable price,fast delivery.
f. We are the source of goods,keep sizable inventory of gaskets & plates to ensure delivery time.Â
g. ISO9001 & ISO14001
Providing Plate and Gasket for Full Makes
Production Line
Making plate mould -Pressing replacement plates-Punching plate holes
-Testing plate corrugation depth- Testing plate crack-Assembling PHE. is specialized in manufacuturing plate heat exchanger,
plate and shell heat exchanger,plate heat exchanger plate,plate heat exchanger gasket and hydraulic press for forming plate.
We can also provide plate heat exchanger mould,semi-welded plate heat exchanger,wide gap/free-flow plate heat exchanger.Â
Quality check
Plate testing:
First, testing plate corrugation depth (free channel).Use micrometer (the best digital displayer) to test 32 sites of plate.Second, testing plate crack.The method is dye check. Spraying display agent (white) on one side of plate,the other side of plate sprays penetrant (red) , if penetrant passes through plate and the side of display agent is dyed red, it shows the plate has crack, the method is very simple and efficient.
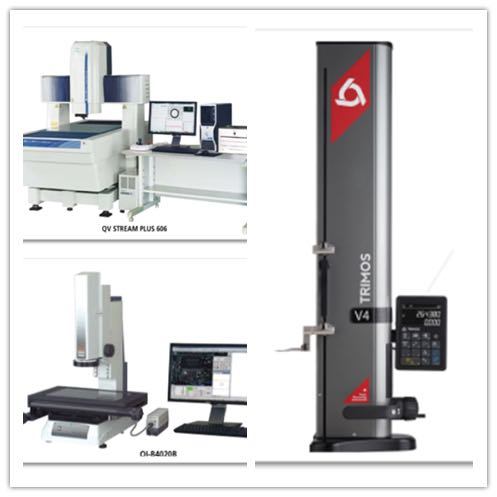
Shipping & Packing
Delivery time: Within 10 working days after received the deposit and confirmed all details.
Package details: Standard export plywood case & customizingÂ
LINA Extrusion Pelletizer
LINA extrusion pelletizer is in the leading level in domestic industry, LINA produces different types granulation extruder such as hot-cutting and air-cooling mode, under-water pelletizing mode, water strand extrusion pelletizing mode and water ring extrusion pelletizing mode to meet the needs of different material.
Material feeding is an important process of the whole granulation process. To achieve effective and efficient material feeding process, LINA adopts twin-taper and twin-arm feeding methods to meet the needs of all kinds of materials.
LINA Twin-Taper Granulation Machine
LINA twin taper granulation machine, it is also called double-cone pelletizing machine, which adopts forced feeding by the two tapers. In order to achieve the continuous and fully automatic process by forced feeding the mixed metal lump, LINA double cone pelletizer reduces the crushing links which exists in traditional granulation of metal powder. LINA twin taper granulator is specialized for the pelletizing of high-hardness, strength and wear resistance material, including stainless-steel powder, iron powder, magnetic powder, zirconium oxide and ceramic powder.
LINA Rubber & Plastic Pelletizing Production Line
LINA rubber & plastic granulation production line is applied for a variety of rubber masterbatch, rubber additives, chemicals auxiliaries and other masterbatch granulation. The whole process is Dispersion Kneader → Automatic hoist → Forced dual-arms feeder → Single screw extruding granulator → Dropping type-air cooling die face hot cutting granulator →Level 1 cooling separator → Level 2 cooling separator → Level 3 cooling separator →Taiwan Transparent vibration distribution sieve → Storage bucket.
Advantages of LINA Granulation Extrusion Line (Main techniques and drawings are from Taiwan, Japan and so on.)
1. The unit has the whole unit process chain, sound and light failure alarm and fast lock fault point and other control functions. All parts that are in contact with the material are made of stainless steel.
2. High accuracy of temperature control system to ensure the temperature sensitivity of the material.
3. It adopts the drop type separating method after cutting process, to avoid Particle agglomeration and ensure particle cooling.
4. Feeding system of the pressing machine adopts heater and reversing device to solve problem of power outage, material crash and cleaning.
5. Especially, the barrel and die head adopts advanced foreign techniques to ensure and control the dangerous occurred when the pressure is uncontrollable. The honeycomb filter plate is easy to clean and quickly change the mesh and the die head t easy to leak.
6. The hoist adopts automatic return technology to ensure the working efficiency.
7. The technological combination of dual-pull forced feeder and single screw not only meet the high requirement of secondary continuous mixing, but also solve the problem of time and power consuming of traditional working process.
Specifications of LINA Extrusion Pelletizing Line
Name |
Mode |
Capacity of Kneader |
Screw length to diameter ratio |
Screw diameter |
Dimension |
LINA Extrusion Pelletizing Line |
LN-10/70 |
10L |
12:01 |
70mm |
2200*1000*1150 |
LN-10/75 |
10L |
12:01 |
75mm |
2650*1100*1250 |
|
LN-35/100 |
35L |
12:01 |
100mm |
3800*1090*1690 |
|
LN-55/120 |
55L |
12:01 |
120mm |
3800*1090*1690 |
|
LN-75/135 |
75L |
12:01 |
135mm |
3850*2350*3280 |
|
LN-110/150 |
110L |
12:01 |
150mm |
5100*2000*1500 |
|
LN-110/165 |
110L |
12:01 |
165mm |
5100*2000*1500 |
Extrusion Pelletizer
Plastic Pelletizer,Plastic Granulation Line,Plastic Extruder,Plastic Extrusion Pelletizer
LINA Machinery Industrial Co.,Ltd , https://www.linakneader.com