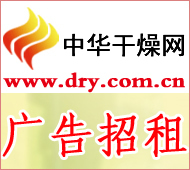
Jiangxi Zhongbang Titanium Industry Co., Ltd. ordered a flash dryer for the drying of rutile titanium dioxide. Flash dryer mainly consists of air intake system, heating system, feeding system, drying host, dust collection system, exhaust system, control system and other components. During work, the wet material enters the drying chamber through the screw feeder, and the material meets the hot air rotating at a high speed in the drying chamber. The fine powdery material is moved to the upper end of the drying chamber by the hot air, and the material that cannot be carried falls on the bottom of the drying chamber. Smashed by the bottom of the smashing device, the material is rapidly dispersed, and the contact area between the material and hot air increases rapidly. Under the action of centrifugal force (classification device at the top), the product that reaches the degree of drying and a certain degree of fineness is blown out of the classification device, and the material is rapidly dried in this process.
Flash dryer has the advantages of high technology content, high standardization, environmental protection, safety, low consumption, simple maintenance, etc. On the design structure:
1 The bottom of the dryer is provided with an inverted cone structure, so that the cross section of the drying gas gradually expands from bottom to top, the bottom air flow is relatively large, the upper air flow is relatively small, so as to ensure that the lower large particles are in a fluidized state while the upper one is small The particles are also in a fluidized state, and the hot air is rotated along the vertebral body to increase the bottom wind speed, shorten the length of the cantilever part of the agitator shaft, increase the safety and reliability of operation, and enable the bearing to be placed outside the machine to effectively prevent the bearing from being exposed to high temperatures. Area work to extend the life of the bearing.
2 The scraper is set on the stirring teeth, and the material is thrown toward the wall at the same time as the material is being crushed by the stirring teeth, and is adhered to the wall surface. If it is not scraped off in time, the equipment may vibrate in severe cases and even cause the stirrer not to turn . A scraper is set on the stirring teeth, so that the material sticking to the wall can be peeled off in time to avoid sticking the wall.
3 The number of rotations of the stirring shaft is controlled by a stepless speed-regulating motor. According to the product particle size requirements to choose different speed, the faster the speed of the stirring shaft, the smaller the particle size of the product.
4 The classifier is installed in the upper part of the dryer. By changing the hole diameter of the classifier and the height of the classifying section, the air flow rate can be changed to control the size and quantity of particles leaving the dryer, the final moisture content, and the residence time of the material in the drying section.
5 Feeder screw conveyor speed is controlled by the inorganic speed motor. The feed rate is controlled according to the material properties and drying process parameters.
6 The equipment has a compact structure, a small footprint, and integrates drying, smashing and grading. It is an organic combination of swirling technology, fluidization technology, spouting technology and convection technology. It does not need to be crushed and sieved after drying, simplifying The production process saves power and equipment costs.
As a new type of equipment, flash drying has been widely used in the titanium dioxide industry in recent years. Currently used in the titanium dioxide industry is the commonly used model 1400, 1600 flash dryer, which can meet the quality requirements of titanium dioxide. In the titanium dioxide industry, the company will continue to adhere to scientific and technological innovation, and constantly improve the company's innovation capabilities, and continuously strive for the sustainable development of the titanium dioxide industry and the drying industry.
A press brake is a piece of manufacturing equipment that is used to bend sheet metal. A press brake is typically narrow and long so that large pieces of sheet metal can be bent by it. A press brake bends sheet metal by lowering a punch onto sheet metal that has been positioned on top of a die. The metal may be bent several times by a press brake until the desired form has been achieved.
Press brakes can make a variety of different bends on many different types of metals. When setting up a bending process, it is important to consider the metal type being bent, the die, the punch, and the bending force.
The metal type is important to understand because of the differing physical properties among metals. For instance, a high carbon steel will generally be less bendable by a press brake than many aluminum alloys because of the differences in ductility and strength. Metals typically have a recommended minimum bend radius that the material can be bent to without damaging it.
The die and the punch used on the press brake both have a large impact on the bending process. The die is hollow material that the metal is placed on top of prior to bending. It is a very hard and strong material that is near in shape to the desired shape of the metal being bent. The punch is a solid material that is lowered down onto the metal. Since the pressing action of the punch onto the metal and the die are what causes the metal to bend, both shapes must be accurately suited to the bending job. The correct metal shape following a press brake operation is dependent on the size and shape of the punches and dies. The dies and the punches are typically designed in such a way that they can be interchanged easily to accommodate a wide array of jobs.
Press Brake,Cnc Press Brake,Metal Bending Machine,Hydraulic Press Brake
Jiangsu Hoston Machine Tools Co., Ltd. , https://www.hostoncncs.com